Kleine Ursache â groÃe Wirkung: Hitzebeständige Rillenkugellager sparen rund 115.000 Euro Kosten pro Jahr
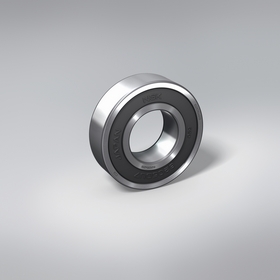
Im Rahmen des AIP-Programms (âAsset Improvement Programâ) berät NSK die Anwender von unterschiedlichsten Maschinen und Anlagen bei der Optimierung der Wälzlagerauswahl. Oft sind es konkrete Probleme, die den Maschinenbetreiber veranlassen, den Rat von NSK zu suchen â so auch im aktuellen Fall eines Herstellers von Konservendosen. Er setzte in einem Durchlaufofen Rillenkugellager mit Staubschutzscheibe ein, deren durchschnittliche Standzeit nur 15 Tage betrug.
Spezialisten von NSK prüften die Einsatzbedingungen der Lager und stellten fest, dass die maximale Ofentemperatur bei rund 300 oC lag. Die Lager selbst erreichten eine Temperatur von 120 oC. Das ist deutlich mehr als die maximale Temperatur, für die konventionelle Rillenkugellager spezifiziert sind. Zudem stellte sich heraus, dass die Umgebungsluft im Ofen durch Lackpartikel verunreinigt ist.
NSK schlug daraufhin den Einsatz von wärmestabilisierten Lagern vor, die bei Temperaturen bis 200 °C einsetzbar sind. Aufgrund der hohen Werkstoffkompetenz gibt es gleich mehrere Werkstoffe im Portfolio von NSK, die sich für den Einsatz unter erhöhten Umgebungstemperaturen eignen.
Auch die Abdichtung der Lager, die jetzt zum Einsatz kommen, ist an die besonderen Bedingungen angepasst. In der Förderanlage des Ofens sind nun Rillenkugellager mit Vitondichtungen montiert, die einen Einsatz der Wälzlager bei Temperaturen bis zu 150 °C ermöglichen. Die Dichtungen halten zudem die Verunreinigungen der Umgebung sehr viel wirksamer zurück als die zuvor eingesetzten Staubschutzscheiben.
Das Ergebnis der Empfehlungen, die der Anwender schnell in die Tat umsetzte: Die durchschnittliche Lagerlebensdauer verlängerte sich von 15 Tagen auf drei Monate. Auch die Lebensdauer des gesamten Bandes verlängerte sich deutlich â von 15 Tagen auf sechs Monate.
Der finanzielle Erfolg dieser ganz einfachen MaÃnahme ist beeindruckend: Vor der AIP-Analyse beliefen sich die Kosten für Ersatzlager und Bandwechsel auf 24.500 â¬. Die Lohnkosten für den Lageraustausch betrugen knapp 2.900 â¬, die Kosten des Produktionsaufall 96.000 â¬. Das sind zusammen 123.400 â¬. Jetzt haben sich diese Kosten auf nur noch 8.400 ⬠reduziert, wobei sich die reinen Anschaffungskosten der Lager auf nur 160 ⬠reduzieren. Insgesamt beträgt die jährliche Einsparung somit 115.000 â¬.