Die Mission: selektive Beschichtung
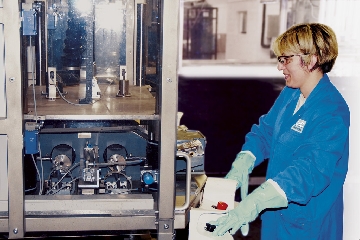
AHC Surface Technology SAS im französischen Faulquemont ist eines von 20 Werken der AHC-Gruppe (www.ahc-surface.com). Schwerpunkt des Geschäftsfeldes der AHC-Gruppe ist die funktionelle Veredelung von technischen Oberflächen als Dienstleistung. Bauteile beispielsweise für die Automobilindustrie, für den Maschinenbau, für die Elektrik und Elektronik sowie für zahlreiche andere Branchen werden mittels patentierter und eigen-entwickelter Verfahren vor Korrosion und Verschleià geschützt oder mit speziellen Eigenschaften versehen. EntwicklungsmäÃig geht der Trend in der AHC-Gruppe hin zu selektiven Beschichtungsverfahren. Bei diesen Verfahren werden nur Teilbereiche eines Bauteils oberflächenbehandelt, ohne aufwändige Abdeckarbeiten.
In der Regel bewähren sich für eine ganze Reihe von Anwendungsfällen klassische chemische und galvanische Tauchbeschichtungen. Einer zunehmenden Anzahl von Anforderungen, bei denen es um eine selektive Galvanisierung geometrisch anspruchsvoller Bauteile geht, werden diese konventionellen Verfahren jedoch nicht gerecht. Hier steht, insbesondere für die Automobilindustrie, mit dem selektiven Beschichtungsverfahren SELGA-COAT® eine wirtschaftliche und umweltgerechte Alternative zur Verfügung.
Im französischen AHC-Werk in Faulquemont (Lothringen) glänzt der Hallenboden in der Werkshalle blitzblank. Nur ein paar Reifenspuren vom Gabelstapler sind zu sehen. Der Geräuschpegel ist niedrig und dennoch wird emsig gearbeitet. âWir haben kleine Beschichtungsinselnâ, erläutert Céline FUNDENBERGER, seit 2003 Betriebsleiterin der AHC Surface Technology SAS in Faulquemont. âWir beschichten an flexiblen Anlagen selektiv Aluminium-Bauteile für die Automobilindustrie nach dem SELGA-COAT®-Verfahren.â Bei AHC in Frankreich bestimmt diese innovative Technologie voll und ganz das Tagesgeschäft.
Bei der typischen Badbeschichtung werden Bauteile in einem groÃen Elektrolyt-Tauchbad unter Stromeinwirkung beschichtet. Beim SELGA-COAT®-Verfahren wird das Aluminiumbauteil hingegen nicht in einen Elektrolyten getaucht, sondern in ein Beschichtungswerkzeug gelegt. Die Elektrolytflüssigkeit bewegt sich mit hoher Geschwindigkeit zwischen dem als Anode geschalteten Bauteil und der Kathode. Integrierte Abdichtsysteme sorgen in dem speziell angefertigten Werkzeug dafür, dass der Elektrolyt in definierten Teilbereichen zirkuliert. So wird nur die Funktionsfläche des Bauteils vom Elektrolyten unter Stromeinwirkung umströmt und beschichtet. Das Abkleben der Bauteile entfällt ebenso wie eine mechanische Nacharbeit.
In der Konstruktion des Werkzeuges, das für jeden Anwendungsfall eigens angefertigt werden muss, sowie in der Einstellung der Beschichtungsparameter zeigt sich die groÃe Erfahrung der AHC-Mitarbeiter aus Faulquemont. Das jeweilige Beschichtungswerkzeug wird nach deren Vorgaben extern gefertigt, anschlieÃend von AHC zusammengebaut und an eine der flexiblen, kleinen Anlagen angeschlossen und eingefahren.
Die SELGA-COAT®-Technologie ist inzwischen so weit entwickelt worden, dass bis zu 10mal höhere Beschichtungsgeschwindigkeiten erzielt werden können als beim klassischen Tauchgalvanisieren. Auch die Schichtqualität ist hervorragend.
Zum Beispiel:
⢠Sehr enge Beschichtungstoleranzen
⢠Sehr niedrige Aufrauung nach der Beschichtung
⢠Gute elektrische Isolierung
⢠Sehr gute VerschleiÃfestigkeit
⢠Sehr gute Korrosionsbeständigkeit
Der Elektrolyt ist ebenfalls Kernstück des SELGA-COAT®- Verfahrens und wird auch an andere Unternehmen geliefert, die ihre Bauteile selbst mit SELGA-COAT®-Anlagen beschichten. Denn das SELGA-COAT®-Verfahren wird von der AHC-Gruppe auch in Lizenz vergeben. AHC Faulquemont verkauft SELGA-COAT®-Anlagen und installiert sie vor Ort in den Kundenproduktionslinien. Durch diese fertigungsflussintegrierte Oberflächentechnik werden die Nachteile der traditionellen Fertigung wie z.B. Transportkosten, Zeitverzug, temporärer Korrosionsschutz, eventuelle Beschädigung oder lange Durchlaufzeiten minimiert. So beschichtet beispielsweise das AHC-Werk im polnischen Gorzyce Motorkolben mit von AHC Faulquemont installierten SELGA-COAT®-Anlagen.
Nach den Plänen von AHC Surface Technology SAS wurden bereits 21 SELGA-COAT®-Anlagen gebaut, davon wurden 12 Einheiten nach Deutschland und in alle Welt verkauft: etwa nach Brasilien, China, Indien, in die Türkei oder nach Tschechien. Alle SELGA-COAT®-Anlagen arbeiten im geschlossenen Kreislaufsystem. Dadurch werden weniger Verunreinigungen in den Beschichtungsprozess eingeschleppt als bei klassischen Tauchverfahren. Da die Beschichtung selektiv erfolgt, sind Elektrolytverluste minimal und somit der Elektrolytverbrauch äuÃerst wirtschaftlich.
Das französische AHC-Werk arbeitet heute mit 23 Mitarbeitern für Kunden, die allesamt aus der Automobilindustrie stammen. âNur in dieser Branche werden bisher Bauteile in einer groÃen Stückzahl gefertigt, so dass sich der Bau eines Werkzeuges amortisiertâ, erläutert Céline FUNDENBERGER. Das können dann gut und gerne bis zu 800.000 Bauteile pro Referenz bzw. Teilefamilie und Jahr sein.
Beschichtet werden unter anderem:
⢠Hydraulische Lenkhilfepumpen
⢠Motorkolben
⢠Platten für Stop- & Start-Systeme
⢠Pumpengehäuse
⢠Steuergehäuse
⢠Ventilgehäuse für â ESP-Systeme
⢠Wärmetauscher für AGR-Systeme
⢠Zwischenplatten für Automatikgetriebe
âIm letzten Jahr hatten wir nur vier Reklamationsfälle, die vom Kunden ausgelöst wurdenâ, berichtet Frédéric COURS, der Produktionsleiter, stolz. âDie Ausfallquote liegt unter 0,5 %. Die Kunden schätzen diese Beschichtungsqualität sehr.â
Zum Beitrag